Low Force Friction Welding
Redefining Efficiency in Solid-State Joining

Contract Welding Services
Leverage our contract welding team’s expertise in part and weld development to enhance your production with Low Force.
Low Force Friction Welding Machines
MTI builds Low Force Friction Welding Machines for various applications.
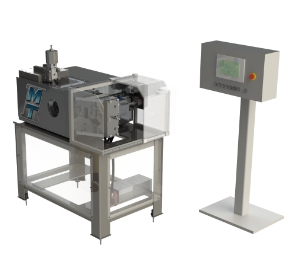
What is Low Force Friction Welding?
Precision Joining with Less Flash Formation
Using our friction welding and solid-state joining knowledge, MTI has developed, designed, and manufactured Low Force friction welding machines that are operating in industry today. But what makes Low Force different from traditional friction welding?
Low Force Friction Welding is a technology in which an external energy source raises the interface temperature of the two joined parts. Unlike traditional methods, Low-Force friction welding significantly reduces the forces needed for a solid-state weld. This approach applies to both linear and rotary processes, offering substantial benefits.
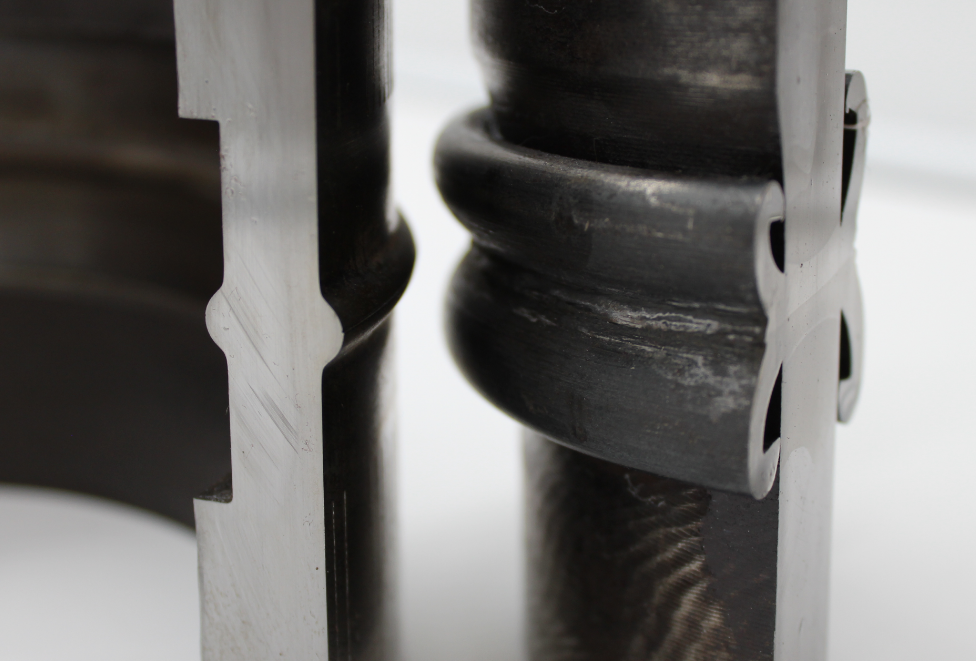
Low Force vs Traditional Friction Welding
Why Low Force Friction Welding
Low Force Friction Welding Handles What Traditional Friction Welding Can’t.
With Low Force Friction Welding, heat and relative motion can be controlled separately which opens the door to new applications including thin-walled parts, hardenable steels, parts that have non-rotational symmetry and other unique geometries. Here are just a few of the benefits Low Force offers.
Solid-State Joining Process
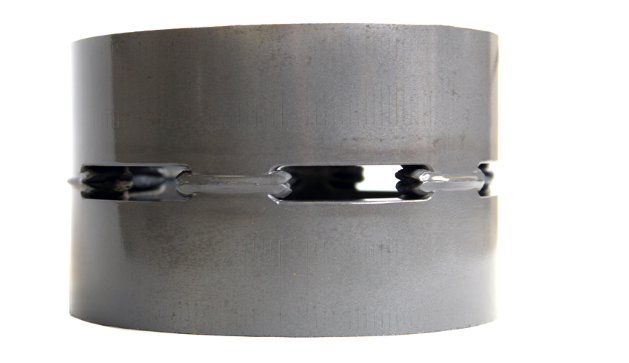
Low Force Friction Welding is a solid-state joining process. Because joining occurs below the melting temperature of the two parts being joined, the weld properties are superior to welds created with fusion processes.
Smooth Flash & Low Upset

As with traditional friction welding, the flash is formed as a smooth bulge instead of a pair of curls. In many cases, this process can achieve welds with little to no loss of length (upset). The shape of the flash combined with the minimal upset creates significant advantages for legacy friction welding applications such as hydraulic cylinder rods and cylinder bodies, drill pipes, and bladed disks. Easier and faster post-weld flash removal, or the elimination of post-weld flash removal altogether, can significantly reduce the cost and increase the throughput of these applications.
Biased Heat for Bi-Metallics
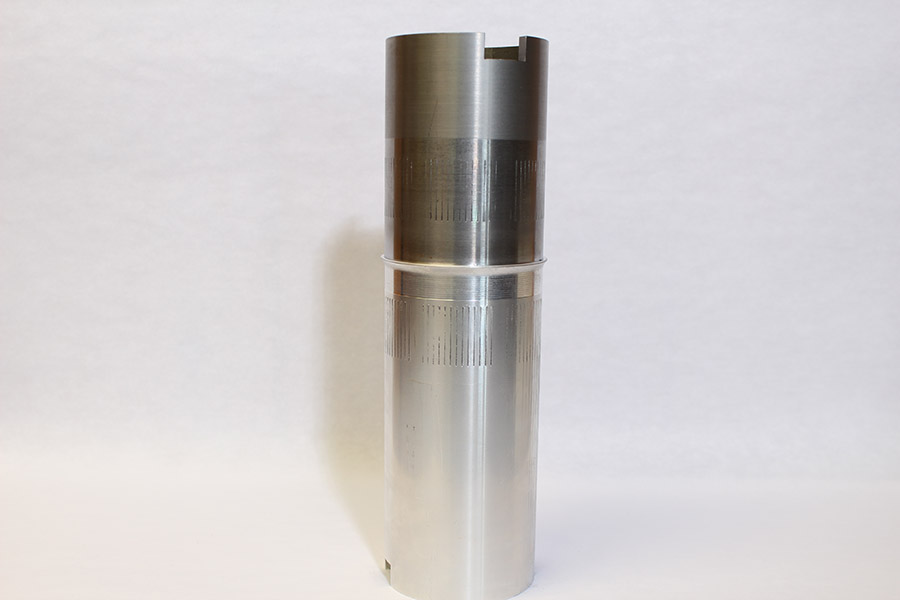
The Low Force friction welding process can independently heat one side of the weld interface relative to the other, which is particularly beneficial when joining bi-metallic components. Biased heating can compensate for the differing yield strengths of materials at elevated temperatures. This provides a more symmetrical consumption of material from the weld interface, even when welding materials with different mechanical properties.
Cooling Rate Control for Hardenable Steels

Post-Weld Heat Treatment in Machine
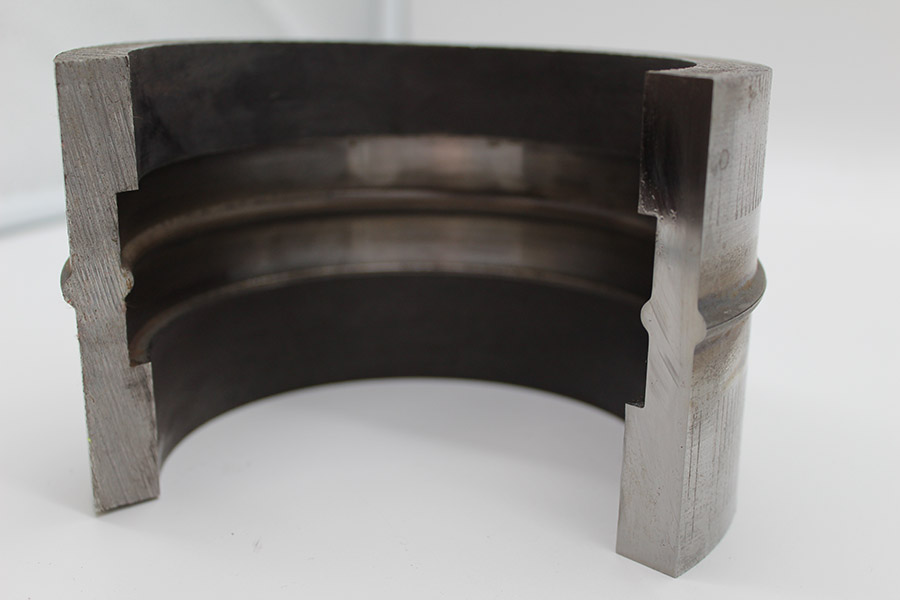
For materials requiring tempering to improve hardness, post-weld heat treatment can be accomplished in the Low Force friction welder without additional machines or steps. In a traditional footprint, we can accomplish multiple processes.
Solid-State Joining Process
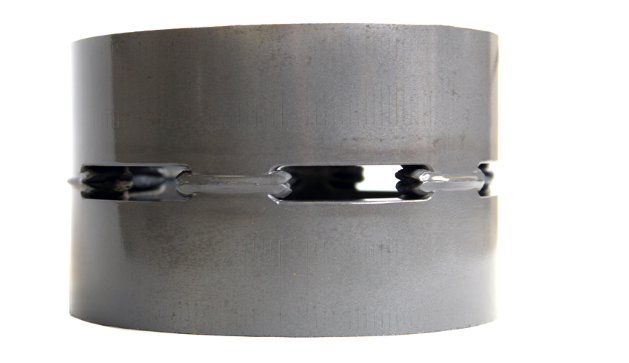
Low Force Friction Welding is a solid-state joining process. Because joining occurs below the melting temperature of the two parts being joined, the weld properties are superior to welds created with fusion processes.
Smooth Flash & Low Upset

As with traditional friction welding, the flash is formed as a smooth bulge instead of a pair of curls. In many cases, this process can achieve welds with little to no loss of length (upset). The shape of the flash combined with the minimal upset creates significant advantages for legacy friction welding applications such as hydraulic cylinder rods and cylinder bodies, drill pipes, and bladed disks. Easier and faster post-weld flash removal, or the elimination of post-weld flash removal altogether, can significantly reduce the cost and increase the throughput of these applications.
Biased Heat for Bi-Metallics
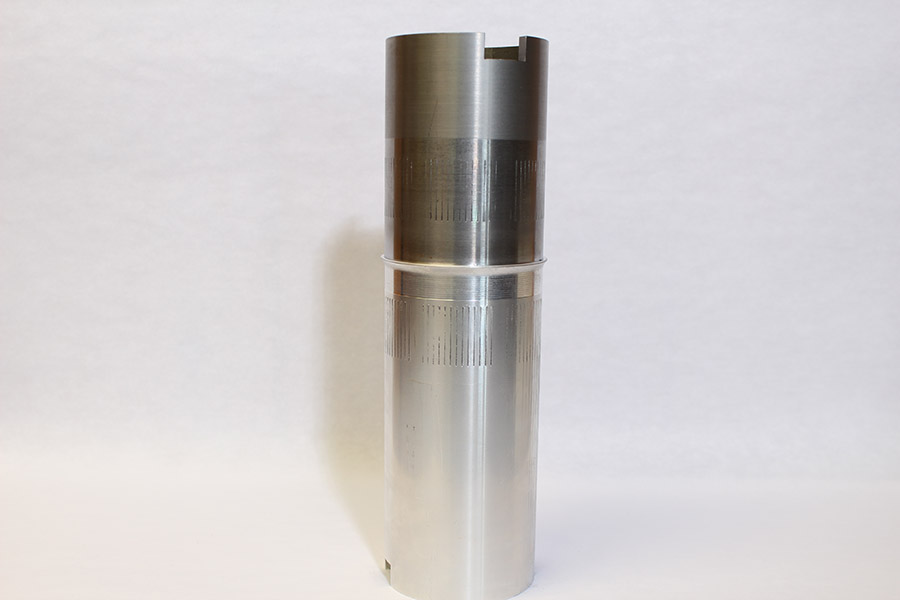
The Low Force friction welding process can independently heat one side of the weld interface relative to the other, which is particularly beneficial when joining bi-metallic components. Biased heating can compensate for the differing yield strengths of materials at elevated temperatures. This provides a more symmetrical consumption of material from the weld interface, even when welding materials with different mechanical properties.
Cooling Rate Control for Hardenable Steels

Post-Weld Heat Treatment in Machine
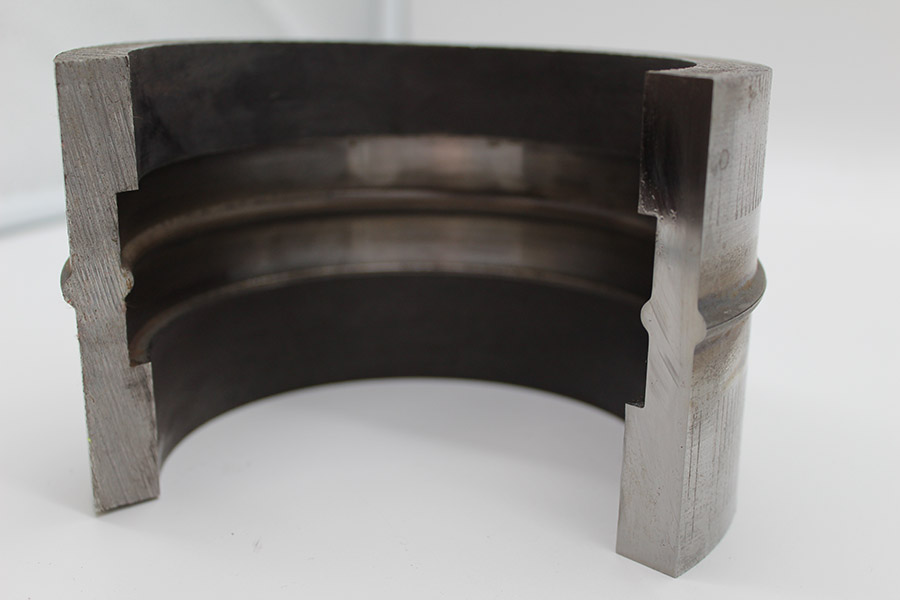
For materials requiring tempering to improve hardness, post-weld heat treatment can be accomplished in the Low Force friction welder without additional machines or steps. In a traditional footprint, we can accomplish multiple processes.
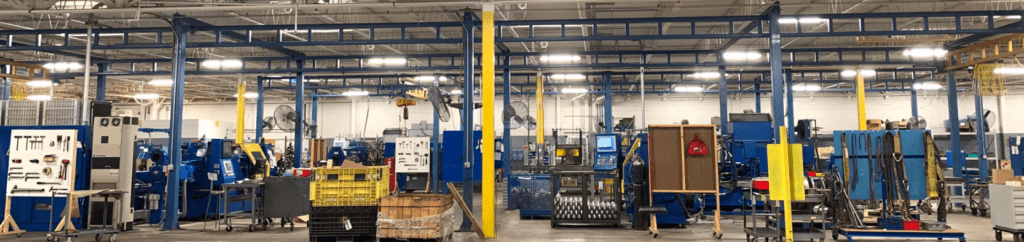
Streamline Manufacturing Processes and Workflows
Low Force is a new process that enables more efficient production methods, making it crucial to evaluate your entire manufacturing process. Questions about part preparation, desired weld characteristics, and post-weld requirements become pivotal. For instance, does your current process involve the removal of flash? If Low Force eliminates this need, you can streamline production by achieving finished parts directly from the welding stage, thereby eliminating additional steps and machinery and optimising floor space utilisation. Ultimately, Low Force has the potential to revolutionise product design and manufacturing workflows, enhancing efficiency and reducing overall production costs.
Part Examples
Low Force friction welding can join a wide range of parts and geometries
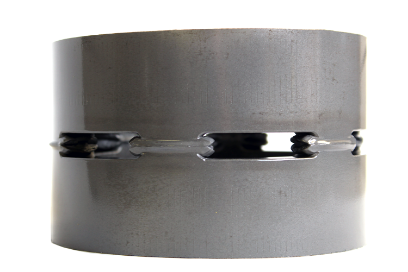
Application
Castellated Tube
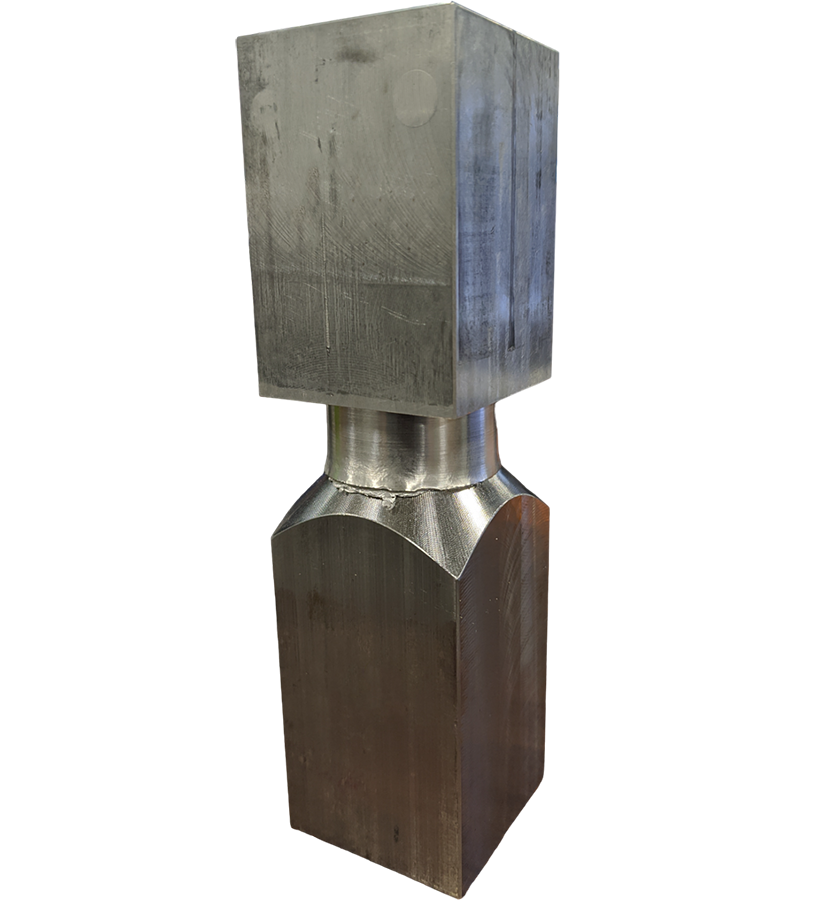
Application
Anode Hanger
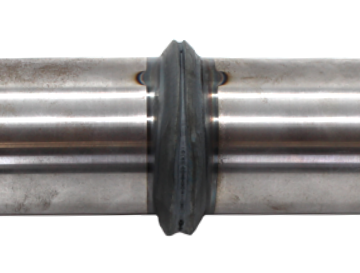
Application
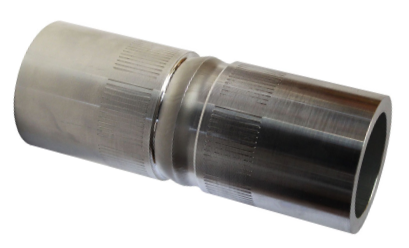
Application
Low Force Tube Development
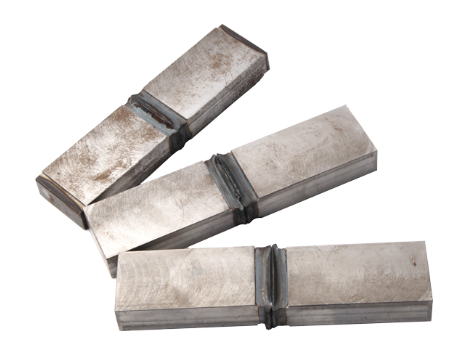
Application
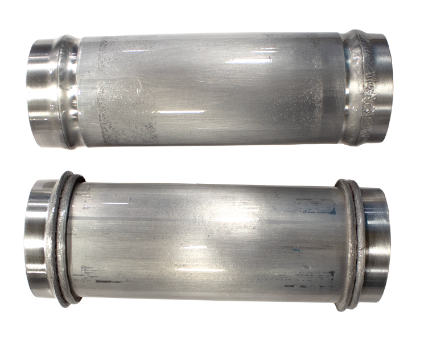
Application
Aluminum Shock Absorber
Contract Welding Services
With various R&D Low Force machines currently operational housed at our US facilities, we can offer comprehensive contract welding services, including part and weld development, to meet your specific needs.
Contract Welding Services
With various R&D Low Force machines currently operational housed at our US facilities, we can offer comprehensive contract welding services, including part and weld development, to meet your specific needs.
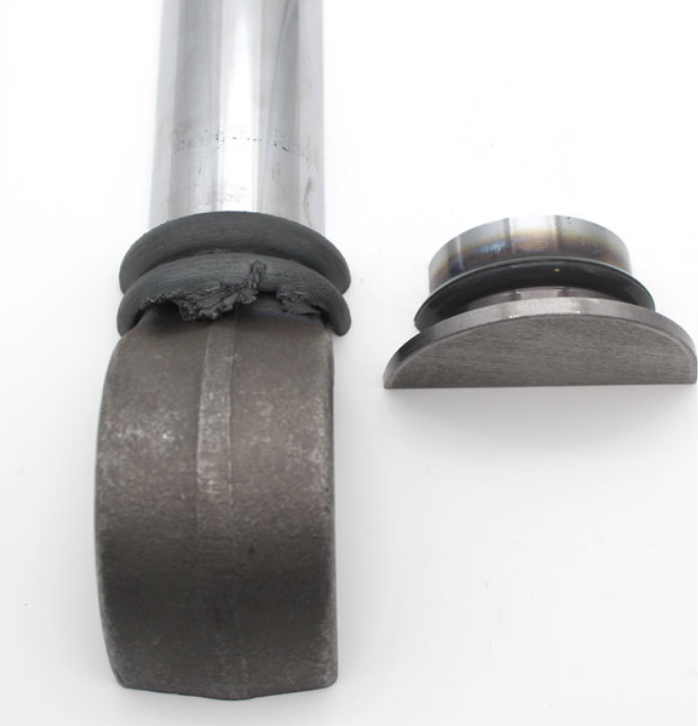
Weld Development 2.0
In this new package, MTI tests the feasibility of your application with traditional friction welding as usual, but we also perform Low Force friction welding test welds so you can compare the benefits of the new technology directly with the traditional friction welding processes.
Check Your Material Combination & Geometry
Can Your Application Be Friction Welded?
Compatible Welds
|
Not Seeing Your Combination Of Materials?
That doesn’t mean it can’t be done. Many of our material combinations are also proprietary. That’s why several of our customers use MTI’s in-house metallurgy lab, which will test your materials for strength and durability to see if friction welding is the right process for you.
Please note Weld strength is dependent on materials & geometry.
Joint Geometries
Friction Welding can join a wide range of part geometries
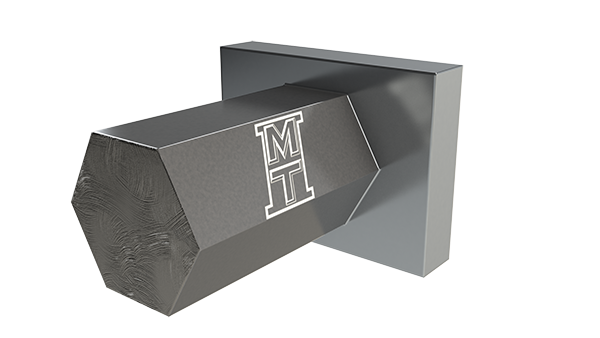
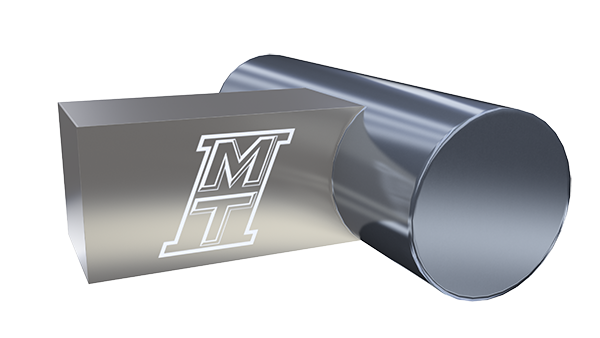
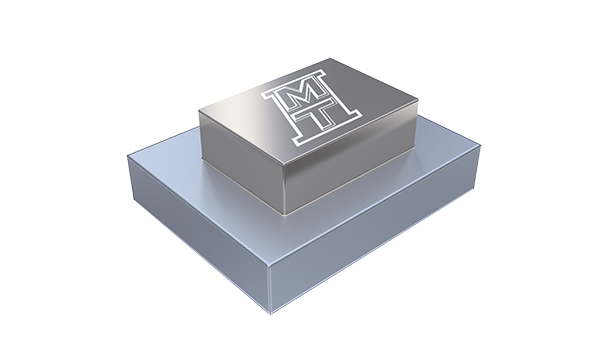
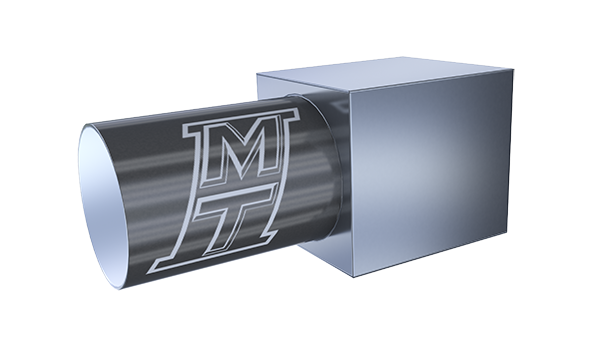
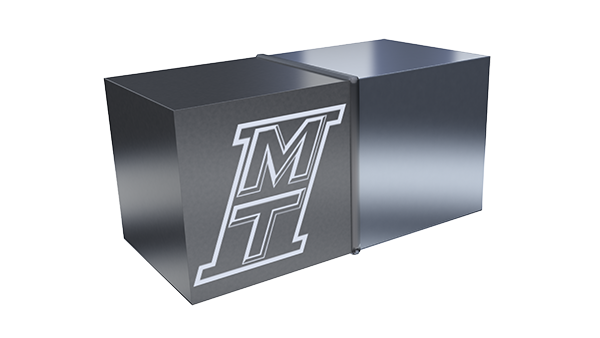
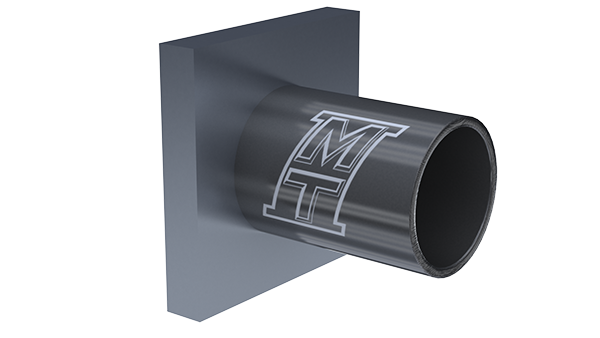
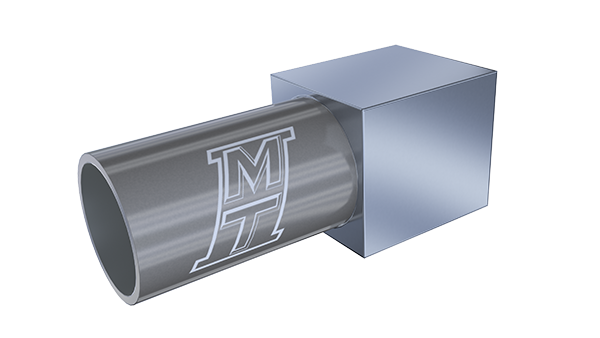
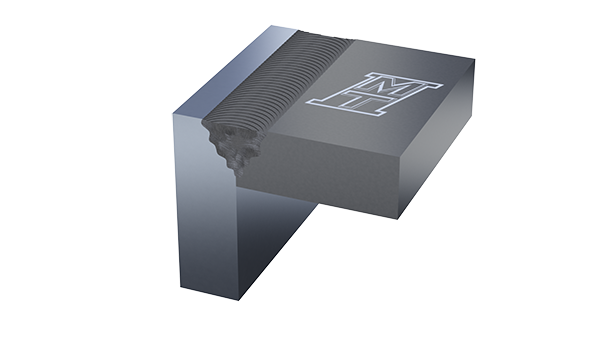
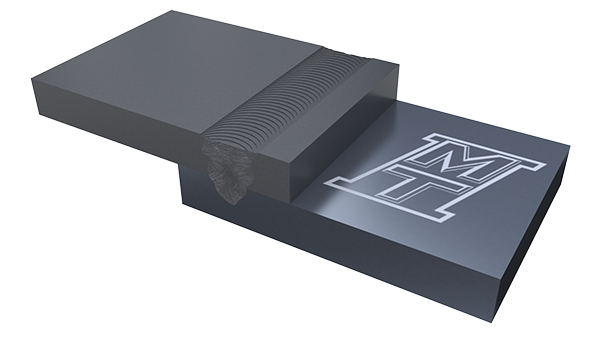
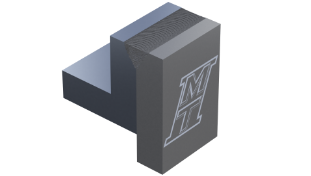
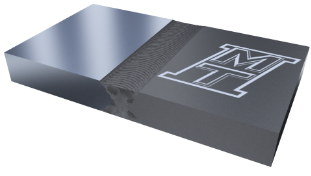
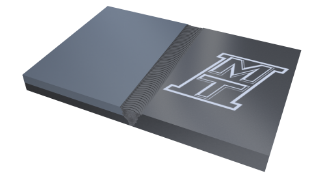
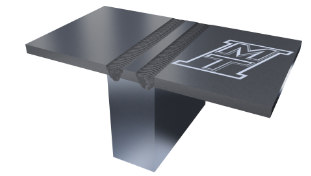
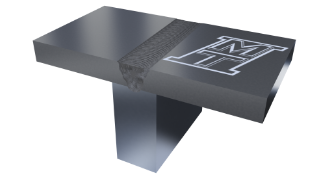
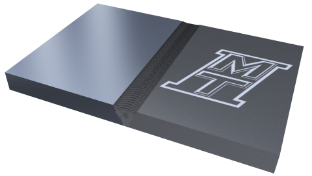
Let’s talk about the specifics of your project:
Learning Center
Case Studies
Videos
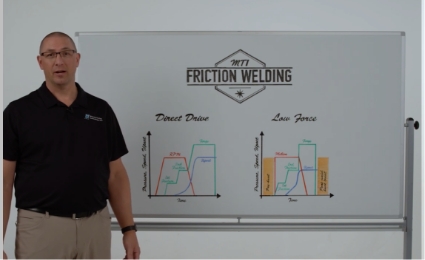
Whiteboard Wednesday
Get the information you need, before you need it — free and straight to your inbox from industry experts.