Contract Friction Welding
From concept to completion
❭ Europe
❭ Europe
❭ Asia
❭ Asia
❭ North America
❭ North America
World Leader in Friction
Welding Technology
World Leader in Friction
Welding Technology
Feasibility Studies & Prototypes
From Feasibility to Full Welding Production
MTI offers contract friction welding services tailored to meet your specific needs. Using our state-of-the-art friction welding machines and managed by our expert global teams, we handle projects of any scale—from small batches to high-volume production. Whether you require precision welding for a few parts or continuous production, MTI ensures quality, efficiency, and reliability.
Contract Friction Welding Services
We Can Help You Reach Your Part Production Goals
Cost Savings
By leveraging MTI’s design expertise during the prototype stage, you can streamline your production process, saving both time and money. With years of development experience and a vast portfolio of successfully welded production parts—many of which began as prototypes—we have the knowledge to guide you on what works and what doesn’t, helping you reach your production goals more efficiently.
Material Evaluations
Our team of in-house experts brings decades of experience, enabling us to provide comprehensive metallurgical testing and evaluations. This ensures the accurate confirmation of physical properties in both the part and the weld zone.
Custom Design Capabilities
Discover new designs and applications without interrupting your manufacturing workflow. We specialise in recommending, designing, and prototyping innovative solutions for product development and enhancement, offering opportunities for additional cost savings and technical improvements to both new and existing designs.
Production Evaluation
Our metallurgy expertise continues even after your part is welded. With our tensile tester and a variety of other strength tests, we ensure that the weld meets your specific requirements and standards.
By leveraging MTI’s design expertise during the prototype stage, you can streamline your production process, saving both time and money. With years of development experience and a vast portfolio of successfully welded production parts—many of which began as prototypes—we have the knowledge to guide you on what works and what doesn’t, helping you reach your production goals more efficiently.
Our team of in-house experts brings decades of experience, enabling us to provide comprehensive metallurgical testing and evaluations. This ensures the accurate confirmation of physical properties in both the part and the weld zone.
Discover new designs and applications without interrupting your manufacturing workflow. We specialise in recommending, designing, and prototyping innovative solutions for product development and enhancement, offering opportunities for additional cost savings and technical improvements to both new and existing designs.
Our metallurgy expertise continues even after your part is welded. With our tensile tester and a variety of other strength tests, we ensure that the weld meets your specific requirements and standards.
Comprehensive Weld Development
Can your materials be joined using friction welding? How does your part geometry affect the process? Our team of friction welding experts is here to help! We focus on optimising your friction welds through a thorough development process. After assessing your materials and producing sample parts, we will provide you with the specifications needed to either commence welding or design a custom friction welder tailored to your project.
Comprehensive Weld Development
Can your materials be joined using friction welding? How does your part geometry affect the process? Our team of friction welding experts is here to help! We focus on optimising your friction welds through a thorough development process. After assessing your materials and producing sample parts, we will provide you with the specifications needed to either commence welding or design a custom friction welder tailored to your project.
Weld Development 2.0
In this new package, MTI tests the feasibility of your application with traditional friction welding as usual, but we also perform Low Force friction welding test welds so you can compare the benefits of the new technology directly with the traditional friction welding processes.
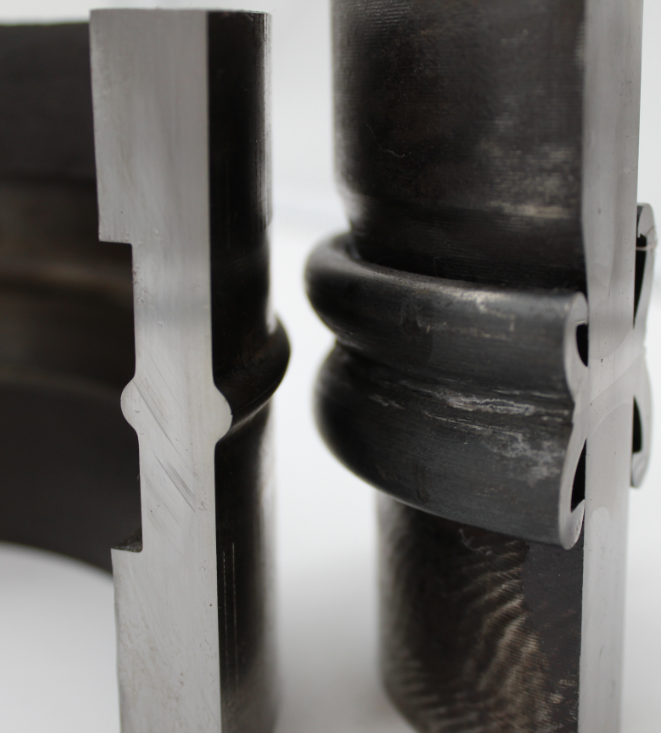
Low Force versus traditional Friction Welding
Friction Welding Concept & Prototype Examples
Manifold Tubing
- Creates narrow heat-affected zone
- 100% bond of contact area
- Resulting joints are of forged quality
- Stronger than parent material
- No weld splatter is created
Finished Clutch Drum
- Dissimilar Materials - 4118 carburized and hardened gear to 1045 Drum
- Greatly increase design flexibility
- Choose appropriate materials and material size for each area of part
- Assembly is complete after welding
Bimetallic Exhaust Valves
- Dissimilar Materials - High temperature resistant valve to high wear resistant alloy stem
- Lower costs as bimetallic application
Stabilizer Bars
- Dissimilar Materials – 4130 Steel tubing with 1018-1020 solid ends welded on each end
- Lightweight, but durable
- Save weight while maintaining torque and fatigue characteristics
Oil Field Valve Body
- Various end fittings inertia welded to standard valve bodies
- Reduces inventory of many different valve body castings
- Replaced single casting
Track Roller Bushings
- Steel backed, bronze laminate thrust washer to steel sleeve
- Reduce raw material and machining costs
- Replaced solid bronze casting
- Annual cost savings after taxes nearly doubled the purchase price of machinery
Lift Screws
- Roll threaded stock, saw cut to length and welded to screw machined ends
- Reduce raw material costs
- Reduction in machining costs
Actuator for Reciprocating Saws
- Mild steel injection molded head (to size)
- Mild steel spindle tube to reduce weight - for directional changes (reciprocating)
- Less cost than a finished product made from a forging or casting
Pre & Post-Weld Process
Our friction welding process goes beyond just welding your parts. It starts long prior to the parts being introduced to our machines and continues beyond their processing. With in-house metallurgical testing and a fully equipped machine shop for pre- and post-weld processes, MTI can take your project from concept to completion entirely in-house. This streamlined approach saves both time and shipping costs by eliminating the need for external resources.
Friction Welding Technologies
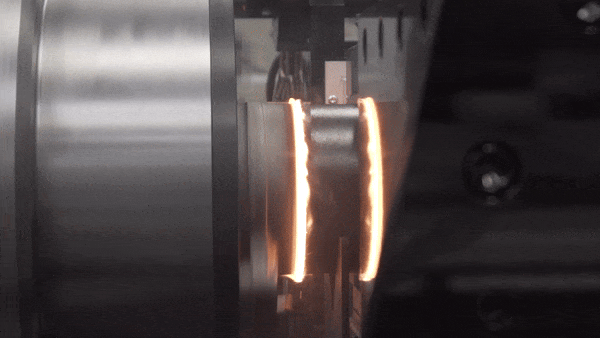
ROTARY FRICTION WELDING
Rotary friction welding (RFW) is a solid-state process where one component is rotated at high speed and pressed against a stationary part. RFW is a widely used technique across several industries, offering unparalleled advantages. Our contract Manufacturing Services facilities have more than 15 combined RFW machines including the world’s largest Inertia contract friction welder.
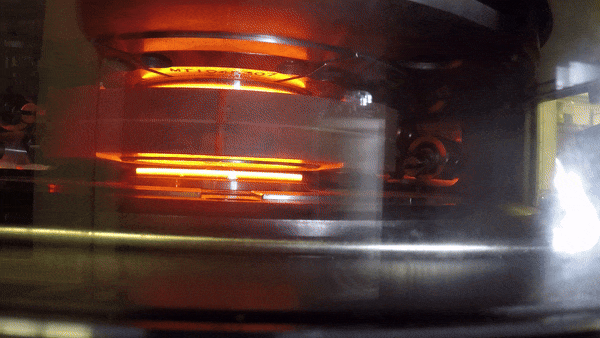
Low Force FRICTION WELDING
Low Force friction welding is our newest solid-state process and utilizes an external heat source to weld the components, reducing the forces required compared to traditional friction welding. Low Force friction welding introduces many benefits across applications including less flash formation, faster weld cycles, and controlled cooling rates. Our contract Manufacturing Services group has 5 Low Force laboratory R&D machines available for your development and production work!

Friction Stir Welding
Friction Stir welding (FSW) is a solid-state process that creates friction by rotating a pin tool into the parts to be joined, stirring the materials together and creating a watertight seal. FSW is becoming increasingly popular following today’s electrification of cars, trains, and planes. Our contract Manufacturing Services group has 4 Friction Stir welders that are ready to handle your R&D and production work.
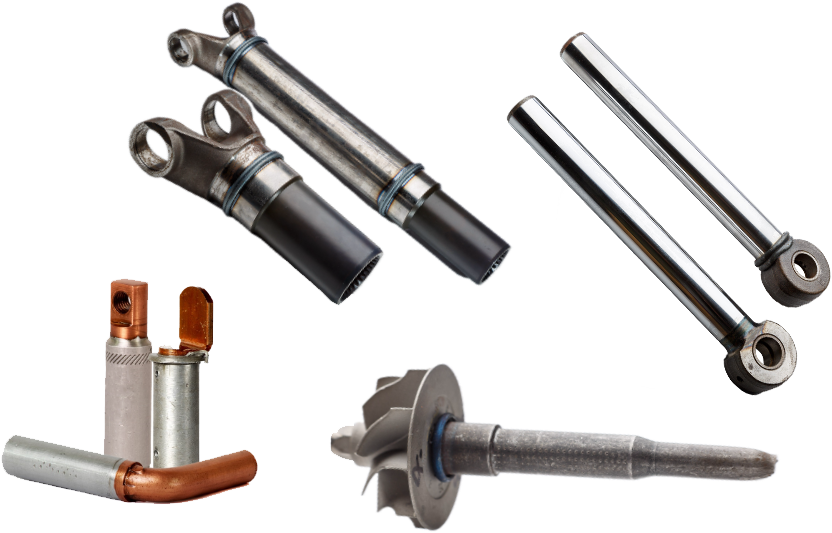
Explore Our Sample Parts
View our sample friction welded parts catalog to uncover applications that might be right for your next project.
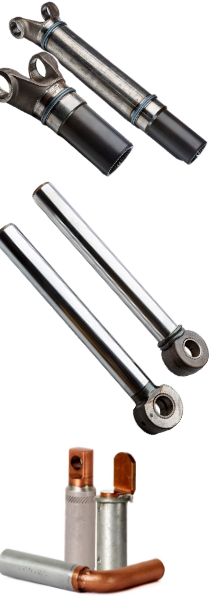
Explore Our Sample Parts
View our sample friction welded parts catalog to uncover applications that might be right for your next project.
Bi-Metallic Joining
From Copper and Aluminum to Steel and Inconel, friction welding allows for the joining of dissimilar metals – and there’s no better place to try out your combination than with our global Contract Friction Welding teams! Allow us to test your materials for strength and durability, and then learn how your combination could benefit your overall process!
Cut Costs, Not Quality
You can save time and money, while also reducing the number of steps to reach your production goal, by taking advantage of MTI’s design experience in the prototype stage. We know what works and what doesn’t, based on our years of development experience and large portfolio of successfully welded production parts – parts that started as prototypes.
Trim Weight Where It Matters
Bimetallic friction welding supports lightweighting goals by using heavier or critical materials only where absolutely necessary. This not only preserves your product’s quality and integrity but also reduces material costs, making your production more efficient and cost-effective.
Unleash Your Part’s Full Potential
Friction welding is an incredibly versatile process, particularly when it comes to joining dissimilar metals. This capability opens up new possibilities for part design and manufacturing, allowing engineers to combine materials with different properties to optimize strength, durability, and weight.
Bi-Metallic With Low Flash & Low Force
The possibilities of joining dissimilar metals can be even broader with our newest solid-state joining technology!
Bi-Metallic Joining
From Copper and Aluminum to Steel and Inconel, friction welding allows for the joining of dissimilar metals – and there’s no better place to try out your combination than with our Contract Friction Welding teams in our US or UK locations! Allow us to test your materials for strength and durability, and then learn how your combination could benefit your overall process!
You can save time and money, while also reducing the number of steps to reach your production goal, by taking advantage of MTI’s design experience in the prototype stage. We know what works and what doesn’t, based on our years of development experience and large portfolio of successfully welded production parts – parts that started as prototypes.
Bimetallic friction welding supports lightweighting goals by using heavier or critical materials only where absolutely necessary. This not only preserves your product’s quality and integrity but also reduces material costs, making your production more efficient and cost-effective.
Friction welding is an incredibly versatile process, particularly when it comes to joining dissimilar metals. This capability opens up new possibilities for part design and manufacturing, allowing engineers to combine materials with different properties to optimize strength, durability, and weight.
The possibilities of joining dissimilar metals can be even broader with our newest solid-state joining technology!
Check Your Material Combination & Geometry
Can Your Application Be Friction Welded?
Compatible Welds
|
Not Seeing Your Combination Of Materials?
That doesn’t mean it can’t be done. Many of our material combinations are also proprietary. That’s why several of our customers use MTI’s in-house metallurgy lab, which will test your materials for strength and durability to see if friction welding is the right process for you.
Please note Weld strength is dependent on materials & geometry.
Joint Geometries
Friction Welding can join a wide range of part geometries
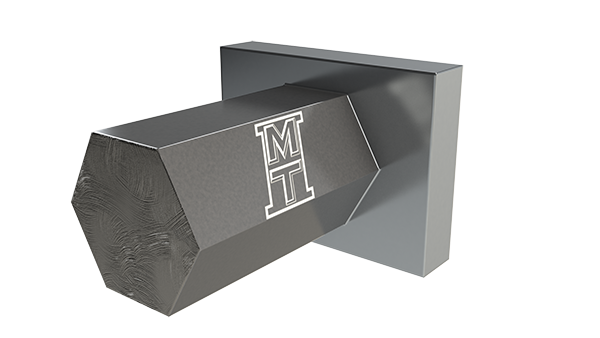
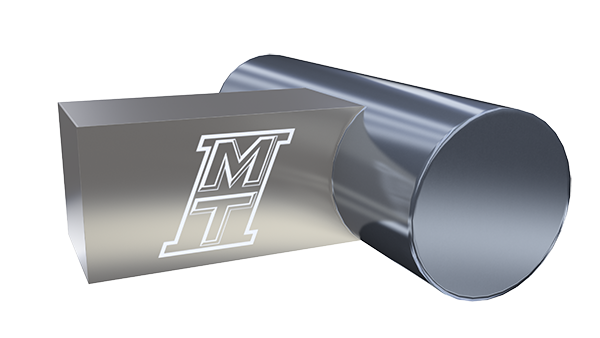
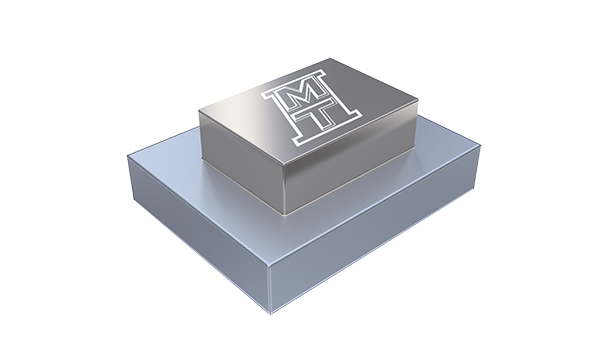
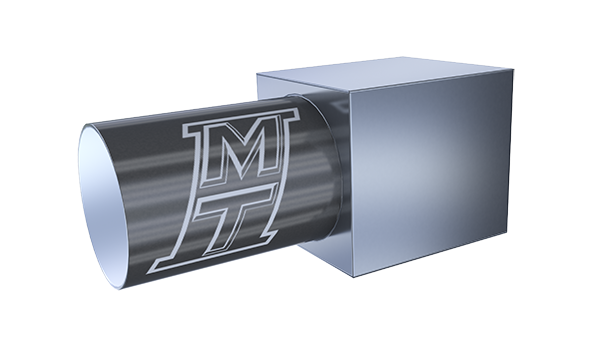
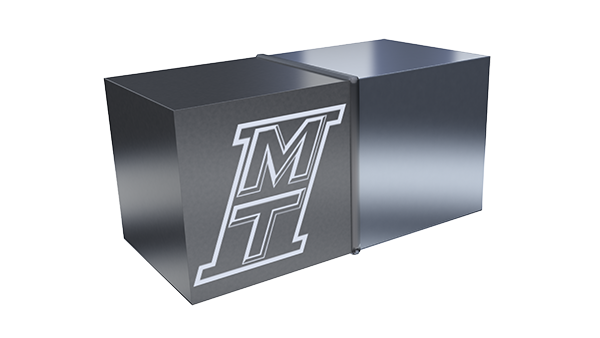
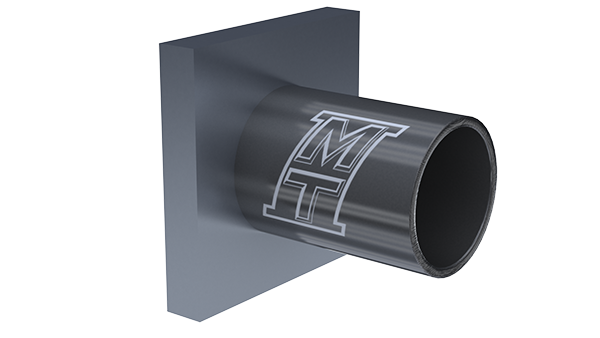
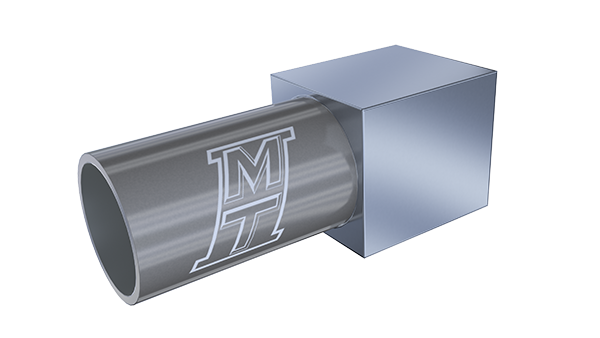
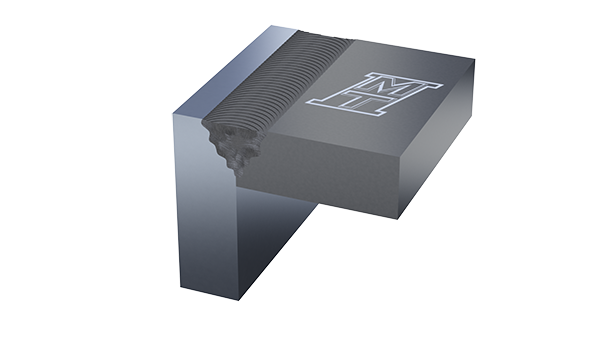
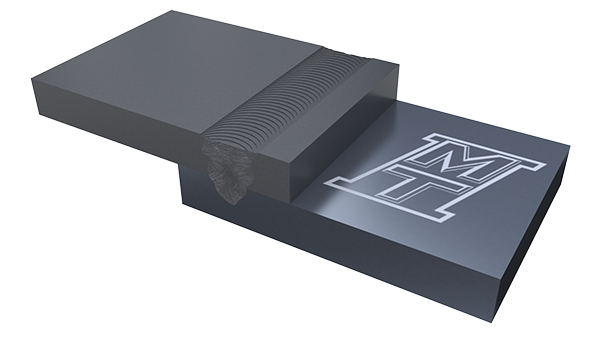
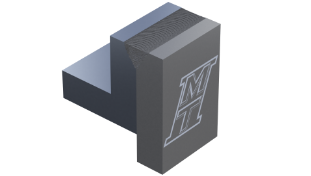
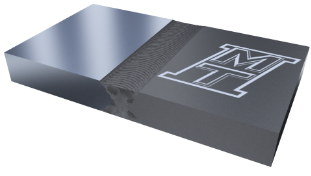
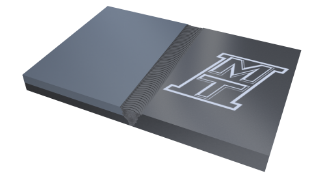
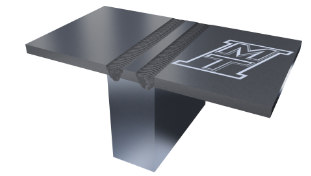
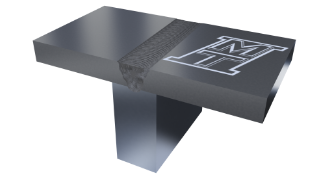
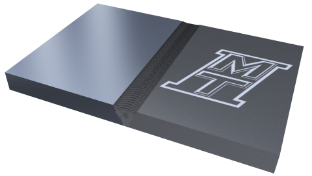
Let’s talk about the specifics of your project:
Production Assurance Program
Our contract friction welding services aren’t limited to customers without their own friction welders. Our team is here to support you if your MTI-built machine is undergoing maintenance, if you’re facing higher-than-usual part volumes, or if your welding program starts before your new machine is installed. We can seamlessly run production to keep your operations moving efficiently.
Learning Center
Case Studies
Videos
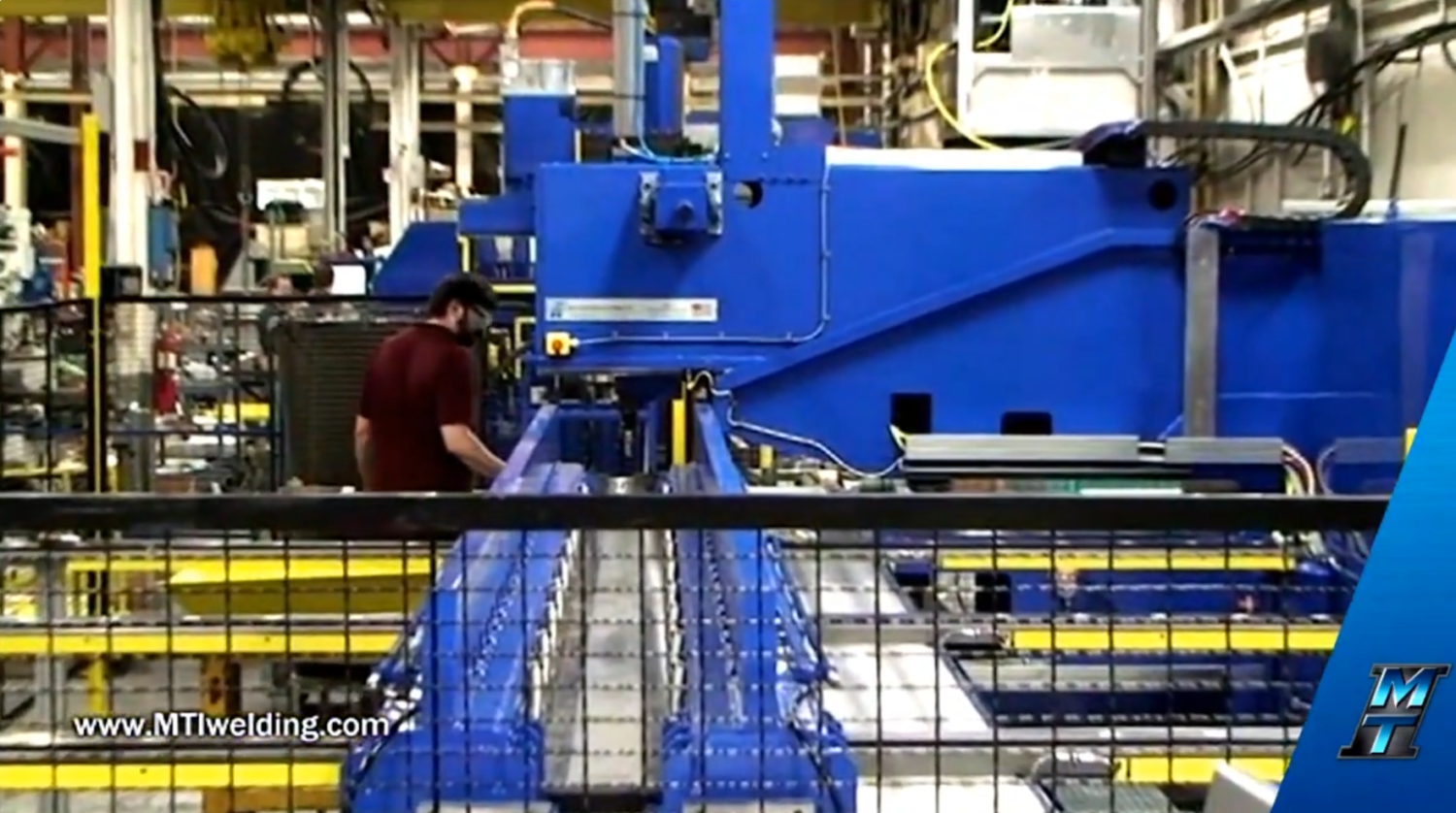
Aerospace Video
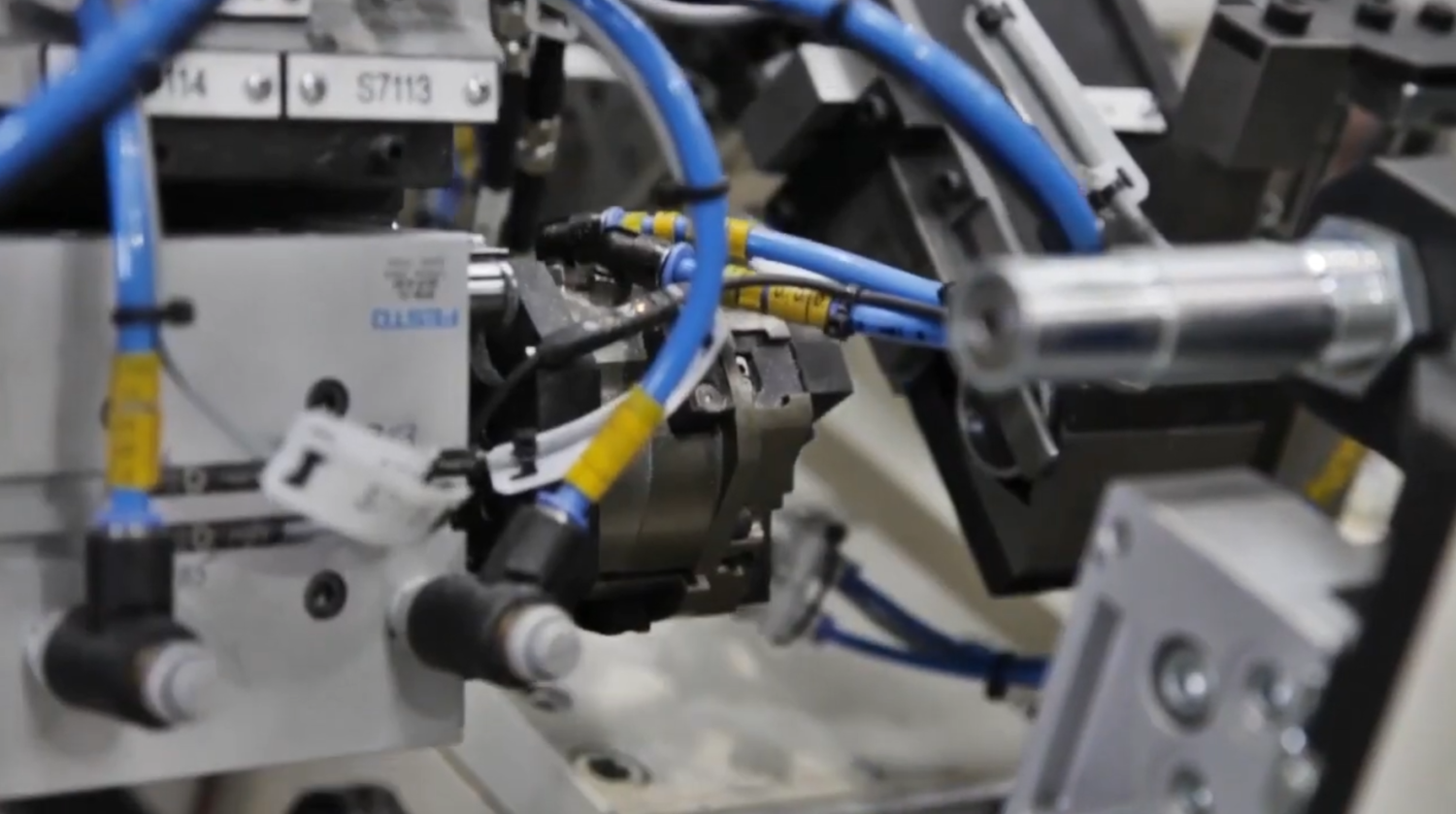
Contract Friction Welding Video
Get the information you need, before you need it — free and straight to your inbox from industry experts.