Innovative Welding for Sustainable Mobility
Friction Welding for Electric Vehicle Components
How MTIW is Making a Difference in the EV Industry
MTI is playing a pivotal role in the Electric Vehicle (EV) industry by providing advanced friction welding solutions that address the unique challenges of EV manufacturing. MTI’s welding technology enables the precise joining of dissimilar materials, such as aluminium and copper, which is critical for components like battery packs and electric motors. By improving the strength and durability of these components, MTI is helping EV manufacturers reduce vehicle weight and increasing efficiency. Additionally, MTI’s automated welding systems can streamline production processes, supporting the scalability of EV manufacturing as demand grows.
Why Friction Welding is Vital for EV Applications
Friction welding is vital for EV applications because it allows for the reliable bonding of lightweight and dissimilar materials, which are crucial for enhancing vehicle range and performance. Friction welding creates high-strength joints without melting materials, reducing the risk of defects and ensuring the structural integrity of components like battery housings, electrical connections, and drive shafts. Furthermore, friction welding’s energy efficiency and minimal waste align with the sustainability goals of the EV industry.
Friction Stir Welding demonstration of an automotive electronics enclosure.
Advantages & Benefits
Powering the Future of Electric Vehicles
At MTI, we’re at the forefront of innovation in the Electric Vehicle industry. Our advanced friction welding technologies offer numerous advantages that are revolutionising EV manufacturing, from enhancing vehicle range to improving sustainability.
Lightweighting
One of the biggest selling points for an Electric Vehicle is its operating range. In other words, the number of miles it can travel before needing a recharge. A heavier car can’t travel quite as far, so that’s why many EV manufacturers place such a strong emphasis on lightweighting. Friction welding can deliver lighter parts by incorporating the use of bimetallics or opting for lighter materials such as aluminium.
Bimetallic Joining
Friction welding gives us the ability to join dissimilar metals, a substantial advantage for lightweighting. Instead of using only one type of metal for a part, manufacturers could switch to a lighter material for a less critical portion of the part and use a heavier material for the heavy-duty portion only. This not only provides substantial performance benefits, but cost savings along the way.
Eco-friendly
The rise of electrification is largely due to the desire to become more sustainable and responsible in our manufacturing practices. Friction welding itself is a green technology that emits no smoke, fumes, or gases and uses no flux or filler material. Additionally, friction welding uses less energy than other joining methods, all of which contribute to a reduction in your carbon footprint and help achieve your going green goals.
Watertight Seals
Friction stir welding delivers parts with watertight seals, ensuring the integrity of battery enclosures and electronic components by protecting them from moisture and environmental contaminants. The solid-state welding process produces high-quality, leak-proof joints without the need for additional sealing materials, reducing assembly complexity and costs. This reliability enhances the safety and longevity of EV components, crucial for maintaining vehicle performance and reducing maintenance requirements.
One of the biggest selling points for an Electric Vehicle is its operating range. In other words, the number of miles it can travel before needing a recharge. A heavier car can't travel quite as far, so that's why many EV manufacturers place such a strong emphasis on lightweighting. Friction welding can deliver lighter parts by incorporating the use of bimetallics or opting for lighter materials such as aluminium.
Friction welding gives us the ability to join dissimilar metals, a substantial advantage for lightweighting. Instead of using only one type of metal for a part, manufacturers could switch to a lighter material for a less critical portion of the part and use a heavier material for the heavy-duty portion only. This not only provides substantial performance benefits, but cost savings along the way.
The rise of electrification is largely due to the desire to become more sustainable and responsible in our manufacturing practices. Friction welding itself is a green technology that emits no smoke, fumes, or gases and uses no flux or filler material. Additionally, friction welding uses less energy than other joining methods, all of which contribute to a reduction in your carbon footprint and help achieve your going green goals.
Friction stir welding delivers parts with watertight seals, ensuring the integrity of battery enclosures and electronic components by protecting them from moisture and environmental contaminants. The solid-state welding process produces high-quality, leak-proof joints without the need for additional sealing materials, reducing assembly complexity and costs. This reliability enhances the safety and longevity of EV components, crucial for maintaining vehicle performance and reducing maintenance requirements.
Our Commitment
Precision Craftsmanship, Outstanding Quality
MTI brings the highest possible degree of safety and quality, whether it’s a part we’re welding or a machine we’re building. We are equipped to produce parts for the most sensitive environments and exacting standards.
Friction Welding Machines for the Electric Vehicle Industry
Electric Vehicles face different challenges than traditional vehicles. But with the right welding machines, engineers and manufacturers can advance to more efficient and environment-friendly vehicles. MTI’s friction welding machines ensures the vehicle’s structural integrity, battery performance, and optimal mileage before the next recharge. Our machines come in semi- and fully automated solutions.
Friction Welding Machines for the Electric Vehicle Industry
Electric Vehicles face different challenges than traditional vehicles. But with the right welding machines, engineers and manufacturers can advance to more efficient and environment-friendly vehicles. MTI’s friction welding machines ensures the vehicle’s structural integrity, battery performance, and optimal mileage before the next recharge. Our machines come in semi- and fully automated solutions.
ROTARY FRICTION WELDING
We specialise in all forms of Rotary Friction Machines, from Direct Drive and Inertia to Hybrid.
LOW FORCE FRICTION WELDING
Produce parts quickly and efficiently with MTI Low Force Friction Welding.
FRICTION STIR WELDING
MTI’s world-class friction stir welding technology ensures water-tight seals and material cost-savings.
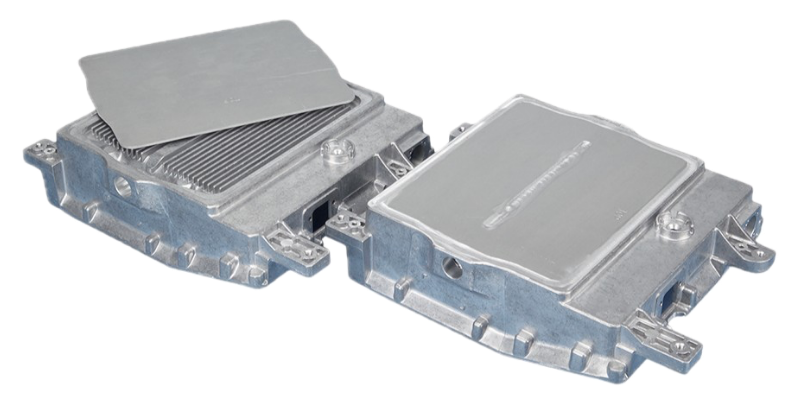
Explore Our Sample Parts
Wondering if your Electric Vehicle components can meet the required shapes and materials? Our sample parts hold the key to your innovation. Explore our samples to find the perfect applications, materials, and geometric fittings for your next Electric Vehicle project.
Contract Manufacturing Services
If you’re needing to have a part designed and manufactured, MTI has state-of-the-art machines and expertise to make it happen. Our global Contract Friction Welding teams handle your project from start to finish, from consultation, design, construction, maintenance, and training.
Contract Manufacturing Services
If you’re needing to have a part designed and manufactured, MTI has state-of-the-art machines and expertise to make it happen. Our global Contract Friction Welding teams handle your project from start to finish, from consultation, design, construction, maintenance, and training.
Learning Center
Featured Articles
Case Studies
Videos
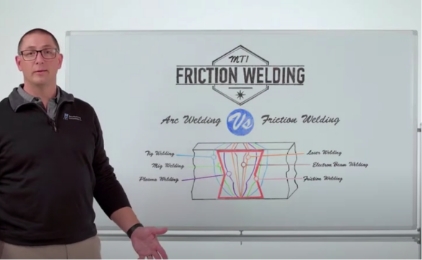
Whiteboard Wednesday
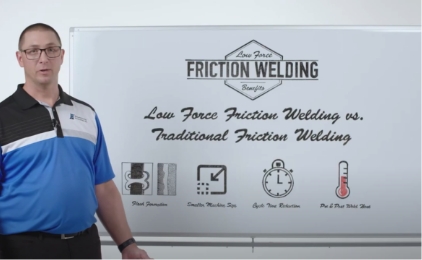
Whiteboard Wednesday
Get the information you need, before you need it — free and straight to your inbox from industry experts.