Welding Innovation for the Road Ahead
Friction Welding for Automotive Components
How MTIW is Making a Difference in Automotive Manufacturing
MTIW’s extensive experience in Automotive welding solutions is evident in the enormous variety of parts our machines produce for many first tier brands. Applications include stabiliser bars, engine valves, pistons, drive shafts, water pumps, axles, airbag inflators, camshafts, U-joints, and many more. MTI helped to pioneer in the changing global requirements for emission standards. Auto manufacturers realised that to do this, the standard aluminium piston would have to be replaced with a newly designed stronger steel piston. In developing their new revolutionary Monosteel piston, client Federal-Mogul knew it needed welding expertise to make it successful, so they turned to MTI. Our Rotary friction welding solutions addressed all design, production, and performance concerns for the Monosteel piston.
Why Friction Welding is Vital for Automotive Applications
Friction welding is highly utilised in the automotive industry as it can be fully integrated into automated production lines to handle the sector’s high volume demands. Advantages such as a full-penetration weld as well as it’s narrow heat-affected zone have made friction welding a key method for joining Automotive applications.
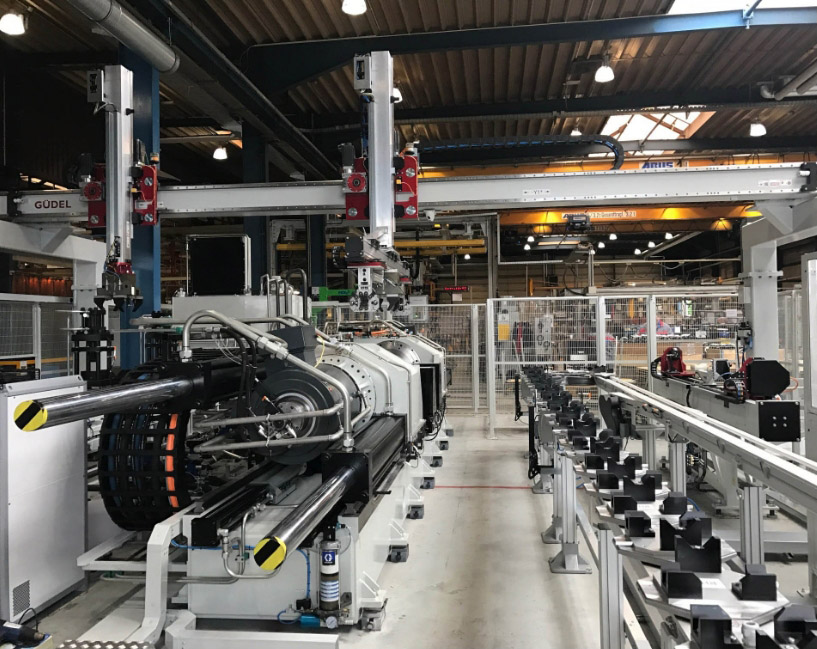
A recent double-ended friction welder for Axles with full automation built at MTIW in Kingswinford, UK.
Advantages & Benefits
Driving Innovation in Automotive Manufacturing
MTI’s cutting-edge friction welding solutions are transforming the automotive industry. Our technologies offer a range of benefits that enhance vehicle performance, reduce costs, and support sustainable manufacturing practices.
Bimetallic Joining
Bimetallic friction welding benefits the automotive industry by enabling the joining of dissimilar metals, optimising the use of lightweight and high-strength materials to enhance vehicle performance and fuel efficiency. This process provides strong, reliable joints without the need for additional fillers or adhesives, reducing manufacturing costs. It also improves corrosion resistance and extends component lifespan.
Lightweighting
Lightweighting with friction welding benefits the automotive industry by reducing vehicle weight through the use of bimetallics, which improves fuel efficiency and reduces emissions. The process creates strong, durable joints without adding excess material, supporting the use of lighter materials like aluminium. This enhances vehicle performance and handling.
Automated, Efficient Process
Friction welding is an automated process that removes the occurrence of operator error resulting in higher process efficiency. Friction welding uses predetermined calculations and measurements, all mechanically operated, that keep quality as consistent as the first weld. Additionally, friction welding cells can accommodate a fully automated work cell with the use of robots and gantry systems.
Green Technology
Friction welding is an eco-friendly technology that does not emit smoke, fumes, or gases. Friction welding does not require consumables such as flux or filler material, reducing your carbon footprint all the way down your supply chain as less material and energy is used.
Bimetallic friction welding benefits the automotive industry by enabling the joining of dissimilar metals, optimising the use of lightweight and high-strength materials to enhance vehicle performance and fuel efficiency. This process provides strong, reliable joints without the need for additional fillers or adhesives, reducing manufacturing costs. It also improves corrosion resistance and extends component lifespan.
Lightweighting with friction welding benefits the automotive industry by reducing vehicle weight through the use of bimetallics, which improves fuel efficiency and reduces emissions. The process creates strong, durable joints without adding excess material, supporting the use of lighter materials like aluminium. This enhances vehicle performance and handling.
Friction welding is an automated process that removes the occurrence of operator error resulting in higher process efficiency. Friction welding uses predetermined calculations and measurements, all mechanically operated, that keep quality as consistent as the first weld. Additionally, friction welding cells can accommodate a fully automated work cell with the use of robots and gantry systems.
"Near-net shape” components can be created through Linear or Rotary Friction Welding, requiring minimal additional machining, saving costly time and materials. Airframe structures and blisks used in jet engine assemblies are two examples of parts created through near-net shape joining.
Our Commitment
Uncompromising Quality, Unmatched Excellence
MTI brings the highest possible degree of safety and quality, whether it’s a part we’re welding or a machine we’re building. We are equipped to produce parts for the most sensitive environments and exacting standards.
Friction Welding Machines for the Automotive Industry
Friction welding machines are renowned for delivering high-volume, consistent-quality welds for components such as brake calipers and transmission gears. Regardless of your project size, our friction welding experts will work with your specifications and feasibility for starting your project or to develop a customised friction welder solution tailored to your needs.
Friction Welding Machines for the Automotive Industry
Friction welding machines are renowned for delivering high-volume, consistent-quality welds for components such as brake calipers and transmission gears. Regardless of your project size, our friction welding experts will work with your specifications and feasibility for starting your project or to develop a customised friction welder solution tailored to your needs.
ROTARY FRICTION WELDING
Our legacy in rotary friction welding, Direct Drive, is the automated solution for parts such as piston rods, axles, and more.
LOW FORCE FRICTION WELDING
Do you need parts joined with minimal flash formation? MTI is the sole company that manufactures Low Force friction welding machines that are still in production lines today.
FRICTION STIR WELDING
Friction Stir Welding is vital for sensitive automotive parts to ensure driving safety. In MTI, we use this type of welding to seal high-strength battery trays and heat exchangers.
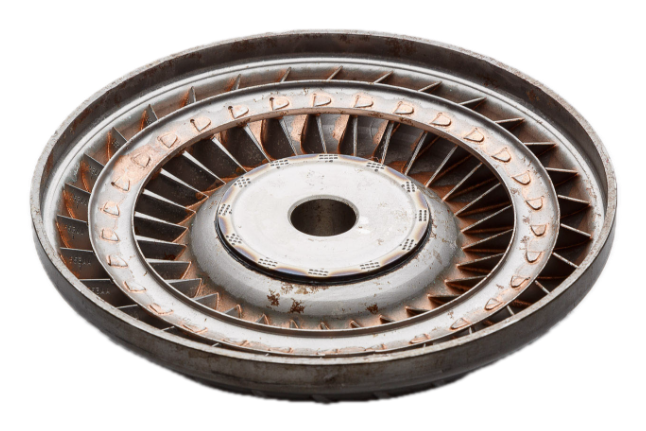
Explore Our Sample Parts
Explore our sample parts to find the perfect applications, materials, and geometric fittings for your next project.
Contract Manufacturing Services
If you have a project in mind, we’re here to optimise your friction welds. We offer everything from an in-house metallurgical lab to a machine shop to help you customise small parts to heavy machinery.
Contract Manufacturing Services
If you have a project in mind, we’re here to optimize your friction welds. We offer everything from an in-house metallurgical lab to a machine shop to help you customize small parts to heavy machinery.
Learning Center
Featured Articles
Case Studies
Videos
Get the information you need, before you need it — free and straight to your inbox from industry experts.