Wheels Up
Friction Welding for Aerospace and Aircraft Components
How MTIW is Making a Difference in Aerospace Manufacturing
As leading global joining solutions providers, MTI regularly works with Aerospace industry organisations from around the world to develop new parts and solutions that are stronger, lighter, resistant to higher temperatures, and more reliable. Through intrinsically understanding the complexities of the sector, MTI is able to anticipate and react to inevitable change within the industry to deliver innovative solutions that adapt over time.
MTI is proud to have built the world’s largest capacity and most innovative, automated, and ergonomically capable Linear friction welding machine. This machine friction-welds critical aircraft engine components to support Pratt & Whitney’s most advanced military programs and next-generation product family.
Why Friction Welding is Vital for Aerospace Applications
The demand for larger and more fuel efficient aircraft means that aero-engines are growing in thrust, temperature, and size. Withstanding the higher temperatures requires critical aircraft and aerospace components made with such materials as superalloy, bimetallic, stainless steel, and aluminium. While these materials can be difficult and many times impossible to weld with conventional methods, they can be joined with the friction welding process. MTI designed Rotary and Linear friction welders of all sizes are in use throughout the aerospace industry, including the largest capacity friction welder ever made.
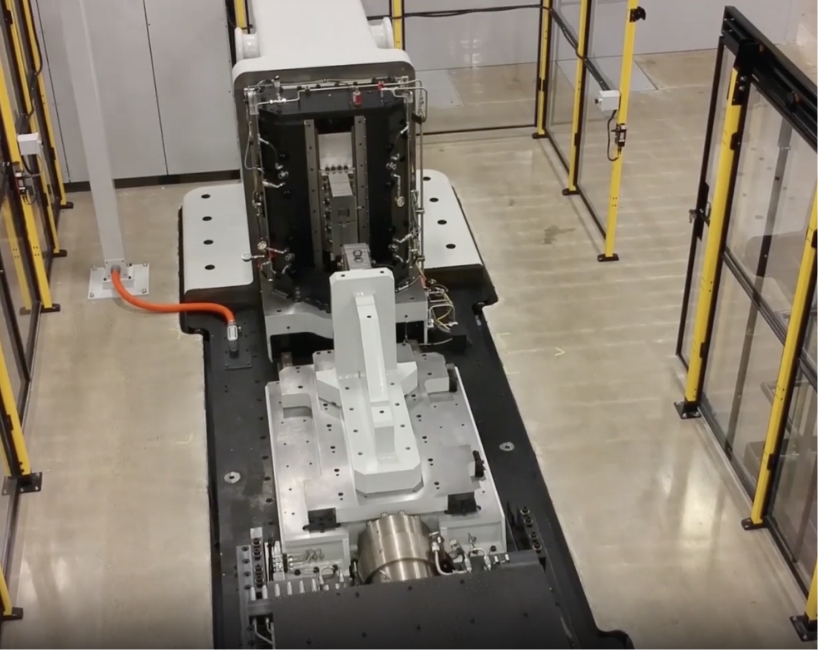
MTI’s LF35-75 Linear friction welding machine available to join to full-scale components.
Advantages & Benefits
Soaring to New Heights in Aerospace Engineering
MTI’s advanced friction welding technologies are propelling the aerospace industry forward. Our innovative solutions offer key advantages that optimise aircraft performance, reduce operational costs, and push the boundaries of aerospace manufacturing.
(Tailored/Close Contour Blanks)
Cut MRO Costs
Cut MRO (Maintenance, Repair, and Operations) costs for aerospace companies with Friction Welding as it provides a strong, reliable joint without the need for additional materials like adhesives or fasteners. This process minimises material waste and reduces the time required for repairs, leading to lower labor costs. Additionally, the improved joint integrity and durability enhance the lifespan of components, resulting in less frequent maintenance.
Lightweighting
Friction Welding opens the door to joining of dissimilar materials, which allows designers to use lighter and/or higher performance materials than traditional joining methods. This allows for reduced weight of parts — and ultimately, better fuel efficiency. These advanced materials require the use of Friction Welding.
Near-Net Shape Joining (Tailored/Close Contour Blanks)
“Near-net shape” components can be created through Linear or Rotary Friction Welding, requiring minimal additional machining, saving costly time and materials. Airframe structures and blisks used in jet engine assemblies are two examples of parts created through near-net shape joining.
Cut MRO (Maintenance, Repair, and Operations) costs for aerospace companies with Friction Welding as it provides a strong, reliable joint without the need for additional materials like adhesives or fasteners. This process minimises material waste and reduces the time required for repairs, leading to lower labor costs. Additionally, the improved joint integrity and durability enhance the lifespan of components, resulting in less frequent maintenance.
Friction Welding opens the door to joining of dissimilar materials, which allows designers to use lighter and/or higher performance materials than traditional joining methods. This allows for reduced weight of parts — and ultimately, better fuel efficiency. These advanced materials require the use of Friction Welding.
"Near-net shape” components can be created through Linear or Rotary Friction Welding, requiring minimal additional machining, saving costly time and materials. Airframe structures and blisks used in jet engine assemblies are two examples of parts created through near-net shape joining.
Our Commitment
Quality is at the core of our ingenuity
MTI brings the highest possible degree of safety and quality, whether it’s a part we’re welding or a machine we’re building. We are equipped to produce parts for the most sensitive environments and exacting standards.
Friction Welding Machines for Aerospace
Friction welding machines designed with the aerospace industry in mind. Explore the capabilities and possibilities of MTI’s line of aerospace friction welders.
Friction Welding Machines for Aerospace
Friction welding machines designed with the aerospace industry in mind. Explore the capabilities and possibilities of MTI’s line of aerospace friction welders.
ROTARY FRICTION WELDING
All mainstream aerospace engine manufacturers utilise and trust MTI-build friction welders for the critical components.
LOW FORCE FRICTION WELDING
MTI is the only company in the world to have developed and designed Low Force Friction Welding machines operating in production today.
LINEAR FRICTION WELDING
MTI is the leading manufacturer to have multiple Linear Friction Welding machines in operation around the globe.
FRICTION STIR WELDING
This solid-state process is ideal for air and space travel because of its lightweighting capabilities and increased strength in the weld seams.
PLUG WELDING
A unique form of friction welding specifically designed to help aerospace companies save on MRO costs.
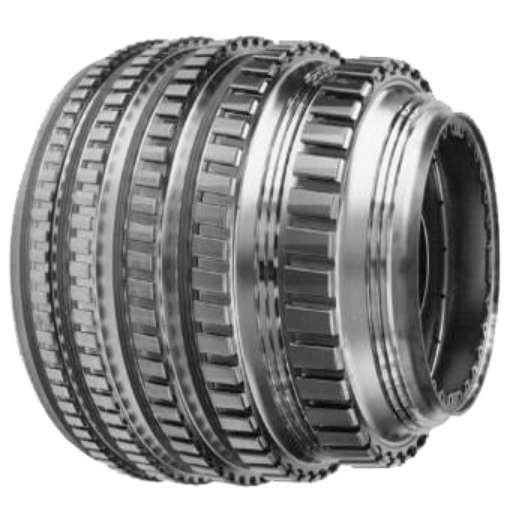
Explore Our Sample Parts
View Our sample friction welded parts catalog to uncover applications that might be right for your next project.
Contract Manufacturing Services
In addition to manufacturing friction welding machines, MTI also operates and welds using our own equipment. Our global contract friction welding teams manage projects from start to finish using our advanced friction welding machines. Whether you need a few parts annually or one part every minute, MTI is here to support your production requirements worldwide.
Contract Manufacturing Services
In addition to manufacturing friction welding machines, MTI also operates and welds using our own equipment. Our global contract friction welding teams manage projects from start to finish using our advanced friction welding machines. Whether you need a few parts annually or one part every minute, MTI is here to support your production requirements worldwide.
Learning Center
Featured Articles
Case Studies
Videos
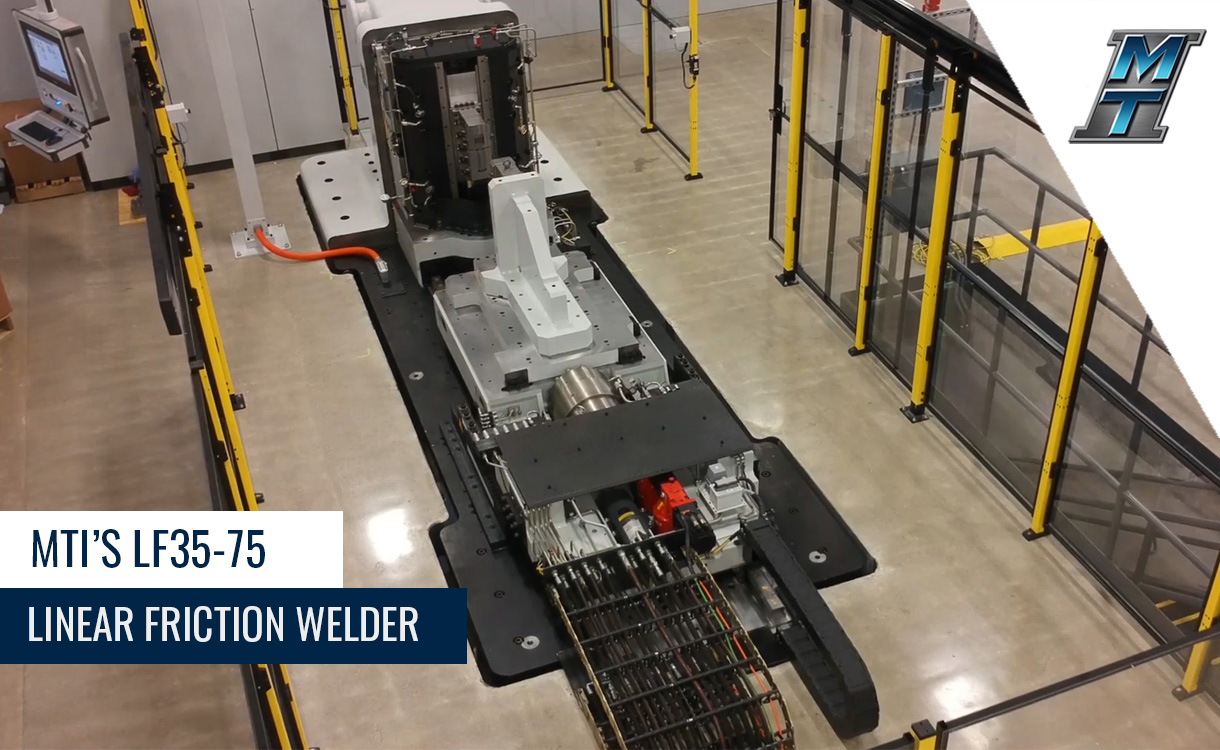
Aerospace Video
Get the information you need, before you need it — free and straight to your inbox from industry experts.